کشش عمیق هیدرومکانیکی ورقهای آلیاژ سبک در دماهای بالا - دانشکده فنی و مهندسی
کشش عمیق هیدرومکانیکی ورقهای آلیاژ سبک در دماهای بالا
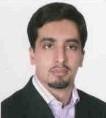
نوع: Type: رساله
مقطع: Segment: دکتری
عنوان: Title: کشش عمیق هیدرومکانیکی ورقهای آلیاژ سبک در دماهای بالا
ارائه دهنده: Provider: سعید یعقوبی
اساتید راهنما: Supervisors: دکتر فرامرز فرشته صنیعی
اساتید مشاور: Advisory Professors:
اساتید ممتحن یا داور: Examining professors or referees:
زمان و تاریخ ارائه: Time and date of presentation: پاییز 1399
مکان ارائه: Place of presentation:
چکیده: Abstract: در پژوهش حاضر، فرآیند شکلدهی ورقی بهروش کشش عمیق هیدرومکانیکی و بهصورت آزمایشگاهی و شبیهسازی عددی در نرم افزار آباکوس مورد بررسی قرار گرفته است. از آنجاییکه برخی از آلیاژهای سبک قابلیت شکلپذیری پایینی در دمای محیط دارند، برای رفع این مشکل، فرآیند شکلدهی آنها در دماهای بالا انجام میشود. بههمین منظور و در ابتدا، فرآیند کشش عمیق هیدرومکانیکی برای آلیاژهای آلومینیم 2024 و منیزیم AZ31B بهصورت تک فلزی انجام گردید. در بخش دوم از این رساله، فرآیند کشش عمیق هیدرومکانیکی برای تولید نمونههای دو فلزی متشکل از فولاد St13- آلومینیم 1200 و منیزیم AZ31B- آلومینیم 1200 صورت پذیرفت. عوامل متعددی بر فرآیند شکلدهی بهروش مزبور تأثیر گذار بوده که در این پژوهش، متغیرهای دما، فشار، فشار پیش بشکه¬ای شدن، قطر اولیه ورق، عمق کشش، شرایط اصطکاکی بین سنبه و ماتریس با ورق اولیه، فاصله بین ماتریس و ورق¬گیر، شعاع نوک سنبه، هندسه سنبه، شعاع دهانه ورودی قالب، لقی بین سنبه و ماتریس، ریزساختار ورق تغییر شکل یافته، میزان سختی در نمونه تولید شده، توزیع کرنش پلاستیک و غیره مورد مطالعه قرار گرفتند. بهمنظور استخراج رابطهای بین پارامترهای بهدست آمده از نتایج شبیهسازی عددی، از آموزش شبکه عصبی مصنوعی استفاده شده و بهینهسازی نتایج بهدست آمده از شبکه عصبی از طریق دو روش الگوریتم ژنتیک و الگوریتم زنبورعسل انجام گرفته است. از مهمترین شاخصهای بررسی کیفیت محصول بهدست آمده در فرآیندهای شکلدهی ورقی، پارامتر بیشینه درصد نازکشدگی میباشد. در پژوهش حاضر، علاوه بر پارامتر مزبور، معیار دیگری بهنام پراکندگی ضخامتی نیز برای بررسی یکنواختی محصول معرفی شده و تأثیر تغییرات پارامترهای اشاره شده در فوق بر این دو شاخص بهصورت جداگانه مطالعه گردیده است. نتایج تحقیق نشان داد که افزایش ضریب اصطکاک بین سنبه و ورق، کاهش ضریب اصطکاک بین ورق و ماتریس و همچنین کاهش فاصله بین ماتریس و ورقگیر باعث بهوجود آمدن محصولی با میزان نازکشدگی کمتر و یکنواختی بیشتر میگردد. از مهمترین عوامل مؤثر در کیفیت محصول، پارامترهای هندسی مجموعه قالب میباشد. مقادیر بهینه شعاع نوک سنبه، شعاع دهانه ورودی قالب و لقی بین سنبه و ماتریس برای ورق آلیاژی آلومینیم 2024 با بهکار گیری آموزش شبکه عصبی GMDH و الگوریتم بهینهسازی زنبورعسل محاسبه شدند. میزان بهبود تابع هدف که ترکیبی از بیشینه درصد نازکشدگی و پراکندگی ضخامتی قطعه کار بود، بهازای مقادیر بهینه پارامترهای هندسی نسبت به بهترین و بدترین مورد از 27 حالت شبیهسازی، بهترتیب 6% و 24% بهدست آمد. مقادیر مزبور نشاندهنده تأثیر محسوس فرآیند بهینهسازی هندسی مجموعه قالب در کیفیت محصولات تولید شده میباشد. فشار بیشینه سیال درون محفظه قالب در طول انجام فرآیند کشش عمیق هیدرومکانیکی، نقش یک نگه دارنده برای ورق داشته و یکنواختی محصول را بهبود می¬بخشد. از آنجاییکه در ناحیه گوشه محصول، قطعه کار بهطور همزمان تحت خمش و کشش قرار گرفته و در این ناحیه کرنشهای نسبتاً بزرگی بهوجود میآید، افزایش بیش از حد فشار سیال موجب افزایش نیروی سنبه و در نتیجه کاهش کیفیت محصول تولیدی (خصوصاً در این ناحیه) میگردد. پس از بررسی مقادیر متفاوت فشار بیشینه سیال، بازه تغییرات این پارامتر بین 5 مگاپاسکال تا 15 مگاپاسکال در نظر گرفته شد. بیشترین تأثیر اعمال فشار پیشبشکهای در ناحیه دیواره محصول رؤیت گردید که بهدلیل التزام وجود لقی در مجموعه قالب آزمایش، حمایتی از طرف سنبه و ماتریس برای قطعه کار در آن ناحیه وجود نداشته و اعمال این فشار اولیه سبب جلوگیری از گسیختگی محصول گردید. بهترین میزان فشار پیشبشکهای برای فرآیند شکلدهی در تحقیق حاضر 1 مگاپاسکال بهدست آمد. با افزایش دمای انجام فرآیند شکلدهی، مواد نرمتر شده و قابلیت شکلپذیری بالایی پیدا میکنند. از طرفی، افزایش بیش از حد دمای فرآیند باعث شده که در محصول تولید شده، بیشینه درصد نازکشدگی افزایش و حتی منجر به پارگی آن شود. دمای مناسب جهت انجام فرآیند شکلدهی ورقی آلیاژ آلومینیم 2024 و آلیاژ منیزیم AZ31B بهترتیب 0C 250 و 0C 200 حاصل شد. ناحیه¬ای از ورق که در هنگام انجام فرآیند بین دیواره مخزن و سنبه قرار دارد، دچار بیشترین میزان کشیدگی شده و کرنش پلاستیک ایجاد شده در این ناحیه بیشتر از سایر نواحی بود. لذا منطقی است که اندازه دانه در ناحیه مزبور نسبت به کف فنجان کوچکتر و بهتبع آن میزان سختی در ناحیه دیواره نسبت به سایر نواحی بیشتر باشد. نتایج بهدست آمده از بافت کریستالوگرافی برای ورق آلومینیم 2024 بر خلاف رابطه هال-پچ بهدست آمد. تصاویر بهدست آمده از آزمون طیف سنجی تفکیک انرژی برای نواحی مختلف از سطح مقطع نمونه آلومینیم 2024 بیانگر آن بود که رسوبات Al2Cu موجود در دیواره محصول، نسبت به سایر نواحی ریزتر بوده و در مرز دانهها با پیوستگی بیشتری پراکنده شدهاند. این نوع توزیع رسوبات، عاملی برای بالا رفتن میزان سختی دیواره در مقایسه با نواحی گوشه و کف فنجان میباشد. نتایج بهدست آمده از رابطه هال-پچ و آنالیز بافت برای ورق منیزیم AZ31B همپوشانی قابل قبولی داشتند. در مورد فرآیند شکلدهی دو فلزی نیز میتوان بیان نمود که با اعمال فشار پیشبشکهای، جدایش بین لایهها در حد فاصل ناحیه در تماس با نوک سنبه و ناحیه فلنج کاهش یافته و میتواند پارامترهای بیشینه کرنش ضخامتی و پراکندگی ضخامتی را بهترتیب تامیزان 57% و 68% کاهش دهد. واژه¬های کلیدی: کشش عمیق هیدرومکانیکی، بیشینه درصد نازکشدگی، پراکندگی ضخامتی، فشار بیشینه سیال، فشار پیشبشکهای، دمای فرآیند، بافت، سختی.
فایل: ّFile: دانلود فایل