An Experimental Investigation on Ultrasonic-Assisted Magnetic Abrasive Finishing with Different Vibration Modes - دانشکده فنی و مهندسی
An Experimental Investigation on Ultrasonic-Assisted Magnetic Abrasive Finishing with Different Vibration Modes
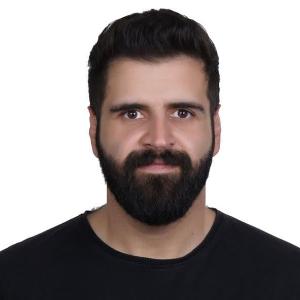
نوع: Type: Thesis
مقطع: Segment: masters
عنوان: Title: An Experimental Investigation on Ultrasonic-Assisted Magnetic Abrasive Finishing with Different Vibration Modes
ارائه دهنده: Provider: payam changaei
اساتید راهنما: Supervisors: Dr Abbas Pak
اساتید مشاور: Advisory Professors: Dr Yahya Choopani
اساتید ممتحن یا داور: Examining professors or referees: Dr Faramarz Fereshteh Saniei, Dr Rahman Seyfi
زمان و تاریخ ارائه: Time and date of presentation: 2025
مکان ارائه: Place of presentation: 54
چکیده: Abstract: Abstract: Today, with advancements in technology and the use of new high-hardness engineering materials, the need for industries to utilize integrated finishing processes to simultaneously increase quality and efficiency has risen. Among the various available methods, finishing surfaces using magnetic abrasive particles has a higher speed and efficiency. In this method, a magnetic field is used to control and displace magnetic abrasive particles. To enhance the performance of this process, especially in components with high hardness, integrated methods such as adding electrolytes in the machining environment (Electrolytic Magnetic Abrasive Finishing) and ultrasonic vibrations are employed. Limitations in finishing insulating workpieces in the Electrolytic Magnetic Abrasive Finishing method and environmental pollution have attracted researchers and industrialists' attention to magnetic abrasive finishing aided by ultrasonic waves. The aim of this research is to investigate the process of ultrasonic-assisted magnetic abrasive finishing through applying vibrations in various modes, including applying vibrations solely to the workpiece (Horizontal-UAMAF), tool (Vertical-UAMAF), and simultaneously to both the workpiece and the tool at different rotational speeds and abrasive particle sizes to evaluate the material removal rate and surface roughness changes. This study experimentally examines the process of ultrasonic-assisted magnetic abrasive finishing by applying vibrations with different modes. An experimental setup has been designed and constructed to apply ultrasonic vibrations to the workpiece (horizontal vibrations) and the rotating abrasive tool (vertical vibrations). Experiments were conducted for various vibration application modes, including applying vibrations solely to the workpiece (Horizontal-UAMAF) and the abrasive tool (Vertical-UAMAF), as well as simultaneously to both the workpiece and the tool (Combined-VHUAMAF) at rotational speeds of 100, 200, and 300 RPM, and abrasive particle sizes of mesh 400, 600, and 800. The material removal rates and surface roughness changes are discussed as outputs of the ultrasonic-assisted magnetic abrasive finishing process under various conditions. The first chapter of this thesis introduces and discusses the applications of magnetic abrasive finishing and the use of ultrasonic vibrations. The second chapter is dedicated to reviewing the literature and research background. The third chapter describes the equipment for generating ultrasonic vibrations, the tools used, and the experimental design for conducting the experiments. In the fourth chapter, the results obtained from the experiments are discussed, and the fifth chapter summarizes the overall research findings and provides scientific suggestions for future research. The results from the experimental tests show that the material removal rate in the applying vibrations to the workpiece along the horizontal axis (HUAMAF) is higher than that in the combined vibration mode (VHUAMAF). The highest material removal rate corresponds to the tool vibrations in the vertical direction (VUAMAF), while the lowest is associated with the condition of no vibrations (MAF). For all vibration modes, increasing the rotational speed of the abrasive tool increases the material removal rate. In the VUAMAF mode, the material removal rate is higher than in other vibration modes at all speeds due to the vertical vibrations creating a pulsating pressure, resulting in greater penetration of abrasive particles into the surface of the workpiece. For the MAF and horizontal vibrations to the workpiece (HUAMAF) modes, the changing speed of the abrasive tool has little impact on the surface roughness variations. However, for the vertical vibration (VUAMAF) and combined vibration (HVUAMAF) modes, at higher speeds, the increase in material removal rate leads to an increase in roughness, thereby negatively impacting the roughness percentage differences. The most significant impact on the roughness percentage changes occurs in the HUAMAF mode. Overall, based on the analysis of variance conducted, it can be concluded that the application of ultrasonic vibrations in the magnetic abrasive finishing process enhances the material removal rate and increases surface roughness changes, with the impact of ultrasonic vibrations on surface roughness being more pronounced. Examination of the surfaces demonstrates that combining ultrasonic vibrations in various modes with the magnetic abrasive finishing process eliminates grinding lines and micro-cracks on the workpiece surface, and the combined ultrasonic vibration mode results in a more uniform surface texture with no visible grinding and finishing lines on the surface.
فایل: ّFile: Download فایل