Determination of mechanical properties of materials by dynamic indentation at high strain rate and high temperature - دانشکده فنی و مهندسی
Determination of mechanical properties of materials by dynamic indentation at high strain rate and high temperature
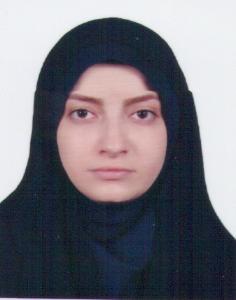
نوع: Type: thesis
مقطع: Segment: PHD
عنوان: Title: Determination of mechanical properties of materials by dynamic indentation at high strain rate and high temperature
ارائه دهنده: Provider: Samaneh Pourolajal
اساتید راهنما: Supervisors: Gholam_Hossein Majzoobi(Ph.D)
اساتید مشاور: Advisory Professors:
اساتید ممتحن یا داور: Examining professors or referees: Ali Alavi Nia-Saeed Feli-Mojtaba Sedighi
زمان و تاریخ ارائه: Time and date of presentation: 2023/february/22
مکان ارائه: Place of presentation: Amphitheater of Technical and Engineering Faculty
چکیده: Abstract: Many engineering components and structures may be subjected to dynamic loading and high temperature. Therefore, knowing the behavior of the material in this type of loading is very important. Various test devices such as tensile and compressive Hopkinson bar, flying wedge and gas gun have been invented to obtain the properties and behavior of the materials under dynamic loading or in other words, at a high strain rate. Unfortunately, many of these devices are complex, expensive and need to be used in special conditions. Therefore, providing practical, quick and cheap devices and methods can have a significant effect on increasing productivity and the speed of extracting results. Indentation test is one of the new, low-destructive, cheap, fast and portable methods to determine the material model and the mechanical properties of materials, which has been used in the last decade to determine some properties of materials such as yield stress and Young modulus. So far, this method has been used to determine the mechanical properties of materials in a quasi-static state. The aim is to generalize and develop the application of indentation test to dynamic loadings and to achieve material properties at high temperatures and strain rates. The basis of this method is extracting the load-depth of indentation curve and converting it into the stress-strain curve of the material. In this project, the dynamic indentation device was designed and built in both fixed and portable forms. Dynamic indentation tests were performed for three alloy materials, steel, aluminum and copper, at four strain rates and four temperatures. In this research, using the experimental results of indentation test, simulation of indentation test and optimization methods (genetic algorithm and particle swarm algorithm) and artificial neural network prediction, the constants of two material models including Johnson- Cook and Zerili-Armstrong, were determined for the three materials. The stress-strain diagrams obtained from indentation test were validated using the stress-strain curves obtained from Hopkinson compression and shot impact tests. An acceptable agreement between the experimental stress-strain curves and the diagrams obtained from simulation and optimization was observed. In general, it can be concluded that the dynamic indentation test can substitute the complex dynamic tests. This study shows that the stress-strain curves obtained from the optimization based on the surrogate model have less error in predicting the stress-strain diagram of the material compared to the curves obtained from the method They had a genetic algorithm with a quadratic polynomial objective function. The results of the artificial neural network showed that the stress-strain curve of the material can be obtained by using the data mines of the behavior of materials that are available on the internet and in the literature. This method, which today is called machine learning and is based on artificial intelligence, along with data mining, can make a revolution in the study of the behavior of materials in the future
فایل: ّFile: Download فایل