Modeling and Investigation of the Ultrasonic Hammering Process on the Surface Properties of Aluminum Alloy - دانشکده فنی و مهندسی
Modeling and Investigation of the Ultrasonic Hammering Process on the Surface Properties of Aluminum Alloy
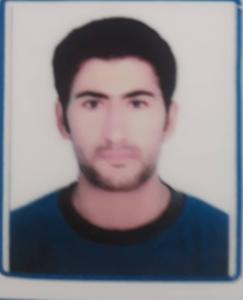
نوع: Type: thesis
مقطع: Segment: masters
عنوان: Title: Modeling and Investigation of the Ultrasonic Hammering Process on the Surface Properties of Aluminum Alloy
ارائه دهنده: Provider: Hamed Samimi
اساتید راهنما: Supervisors: Dr. Abbas Pak
اساتید مشاور: Advisory Professors:
اساتید ممتحن یا داور: Examining professors or referees: Dr. Rahman Seifi and Dr. Hashem Mazaheri
زمان و تاریخ ارائه: Time and date of presentation: 2023.2.7
مکان ارائه: Place of presentation: Faculty of Engineering - Seminar 1
چکیده: Abstract: Aluminum alloys are chosen in various applications due to their special properties and high corrosion resistance. By optimizing the surface performance of aluminum alloys, their overall behavior and reliability can be effectively improved. In recent years, the study of surface mechanical operations has attracted the attention of researchers. Because this operation can significantly improve the surface properties by inducing compressive residual stress and grain modification at the nanometer scale. Various mechanical surface methods have been used to improve the surface characteristics of aluminum alloys. Among these methods, the ultrasonic hammering method is a cold work process in which a large number of blows are applied to the surface of the sample in a short period of time with high frequency. In this research, the effect of ultrasonic hammering process on the surface properties of aluminum alloy Al6061-T6 has been investigated. . First, in order to investigate the conditions of ultrasonic hammering and the effect of pin geometry on the amount and depth of the residual stress, numerical modeling was done with Abaqus software, and after determining the effect of these variables, the appropriate conditions were determined and practical tests were performed. Oscillation amplitude, rotational speed and advance rate have been selected as the input parameters of the ultrasonic hammering process in practical tests. The results obtained from the modeling showed that with the increase in the diameter of the pin, the value of the maximum compressive residual stress decreased and the stress depth increased. According to the numerical modeling, increasing the pin tip radius has increased the compressive residual stress and decreased the stress depth. Also, with the increase of the swing range, the amount and depth of the maximum compressive residual stress have increased. Paying attention to the results of the practical tests, it was observed that the compressive residual stress increased with the increase in the advance rate And the residual stress has decreased with the increase of rotational speed and fluctuation range. In general, the ultrasonic hammering test on aluminum alloy 6061 has increased the surface residual stress from 186 MPa tensile to 197.41 MPa compressive by creating a severe plastic deformation zone Also, by performing ultrasonic hammering, hardness has increased by 158% and wear resistance by 34.48%. Key Words: Ultrasonic hammering, Aluminum 6061, Modeling, Residual stress, Surface properties
فایل: ّFile: Download فایل