The effect of magnetic field on the weldability of dissimilar aluminum/steel joint produced by laser welding process - دانشکده فنی و مهندسی
The effect of magnetic field on the weldability of dissimilar aluminum/steel joint produced by laser welding process
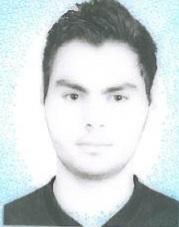
نوع: Type: thesis
مقطع: Segment: masters
عنوان: Title: The effect of magnetic field on the weldability of dissimilar aluminum/steel joint produced by laser welding process
ارائه دهنده: Provider: khashayar Momen
اساتید راهنما: Supervisors: Dr. Mohsen Sheykhi
اساتید مشاور: Advisory Professors: Dr. Mahmood Moradi, Dr. Seyed Alireza Rasooli
اساتید ممتحن یا داور: Examining professors or referees: Dr. Hamid Esfahani, Dr. Abas Pak
زمان و تاریخ ارائه: Time and date of presentation: 2023/09/19
مکان ارائه: Place of presentation: Class 3 of the Faculty of Engineering
چکیده: Abstract: Welding of steel and aluminum is among the crucial processes in the metals industry. In recent years, the use of laser welding as an advanced process for joining different metals has garnered the attention of researchers and industrialists. However, welding steel to aluminum presents significant challenges due to the physical and chemical differences between these two metals. One of the proposed solutions to enhance the laser welding process between these two metals is the utilization of a magnetic field to control and improve welding characteristics. The use of laser technology for metal welding has gained considerable attention in recent decades due to its high precision, minimal heat impact, and reduced need for consumables. In this regard, welding steel to aluminum has become an attractive research topic due to the importance of applications and the high mechanical properties of these two metals. Welding steel to aluminum comes with challenges such as temperature difference, different thermal expansion coefficients, distinct mechanical properties, and the formation of various phases. These differences can lead to the formation of microcracks and weak points in welding, resulting in decreased efficiency and connection stability. Employing a magnetic field as a control factor in laser welding between steel and aluminum can facilitate the improvement of welding properties. This field can aid in controlling heat distribution, regulating cooling rate, and reducing the formation of undesirable phases. In this study, using fiber laser welding, steel AISI 304 and aluminum 1050, as well as steel ST37 and aluminum 1050, were welded, and the effect of the magnetic field on the appearance of the weld pool was examined. Six samples were divided into two groups: "no filler" samples resulting from the connection of steel 304 and aluminum, and "filler" samples resulting from the connection of steel ST37 and aluminum. Each group was investigated both without a magnetic field and with a magnetic field, using welding speeds of 8.8 and 12 mm/s. The S2, S5, and S6 samples were in the "no filler" group, while the S1, S3, and S4 samples were in the "filler" group. Furthermore, samples S1 and S2 were welded without a magnetic field, while samples S3, S4, S5, and S6 were welded with a magnetic field. Samples S3 and S5 were welded with a magnetic field intensity of 70 mT, while samples S4 and S6 were welded with a magnetic field intensity of 120 mT. The welding was performed using a 600-watt laser welding machine for all samples, with a focal distance of 31 mm, a frequency of 5000 Hz, and at the two different welding speeds. Applying a magnetic field has led to an increase in the depth of the welds and a decrease in their width. In samples without a magnetic field, the welds exhibited a wider keyhole-like appearance, while under the influence of the magnetic field, the keyhole holes transformed into V-shapes. The results indicate a significant impact of the magnetic field on the microstructure of the weld. The Lorentz force generated by the magnetic field has displaced the movement of the molten pool, increased the density of surface reactions, and enhanced the microstructure of the weld. Additionally, with an increase in the magnetic field intensity, the metallic compounds in the welded joints were unexpectedly scattered, leading to an improvement in the mechanical properties of the joints. A uniform application of the magnetic field can also prevent the formation of glass-like shapes and enhance the final properties of the connection. These findings suggest that applying a magnetic field in the laser welding process can effectively contribute to controlling and improving the microstructure and properties of the welded joints. Based on the research results, it has been determined that due to the diversity of elements and the formation of intermetallic compounds, steel 304 possesses greater hardness compared to steel ST37. As welding speed increases, the hardness increases in all samples. However, applying a magnetic field leads to a decrease in hardness in the samples. This phenomenon is attributed to better distribution of precipitates and more scattered elements in the presence of the magnetic field, reducing the phase separation. In the steel section, the average hardness is around 250 Vickers, increasing to approximately 550 Vickers in the center. Moreover, in the aluminum section that enters the aluminum sample's depth, the hardness remains nearly constant, indicating around 70 Vickers. Keywords: Laser welding, magnetic field, Lorentz force, steel and aluminum, intermetallic compounds