The effect of mechanical post-treatment applied on the CrN/CrAlN nano-layered coating on the corrosion and tribology behavior - دانشکده فنی و مهندسی
The effect of mechanical post-treatment applied on the CrN/CrAlN nano-layered coating on the corrosion and tribology behavior
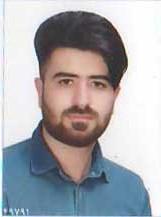
نوع: Type: thesis
مقطع: Segment: masters
عنوان: Title: The effect of mechanical post-treatment applied on the CrN/CrAlN nano-layered coating on the corrosion and tribology behavior
ارائه دهنده: Provider: Amirhosein Ghorbani
اساتید راهنما: Supervisors: Hassan Elmkhah - Arash Fattah alhosseini
اساتید مشاور: Advisory Professors: Mostafa Meghdari
اساتید ممتحن یا داور: Examining professors or referees: Meisam Nouri - Omid Imantalab
زمان و تاریخ ارائه: Time and date of presentation: 24/08/2022
مکان ارائه: Place of presentation: دانشکده مهندسی
چکیده: Abstract: The present research was carried out to investigate the influence of the microblasting process on electrochemical and tribological behavior of the CrN/CrAlN nanolayer coatings deposited on stainless steel 430 substrates using the cathodic arc evaporation physical vapor deposition (CAE-PVD). After deposition, the mechanical post-treatment was conducted by a wet microblasting at three pressures. The coatings were characterized by X-ray diffraction (XRD) and field-emission scanning electron microscopy (FESEM) to determine their morphology and thickness. Rockwell C test was utilized according to VDI3198 to evaluate the adhesion of the coatings to the substrate. The images of this test were then quantitatively assessed. A nano-indentation test was employed to assess the mechanical properties of the coatings. The hardness of the coatings without and with microblasting at the pressures of 2, 4, and 6 bar was 19.19, 21.83, 23.10, and 23.42 GPa, showing 14, 20, and 22% increments, respectively. Ball-On-Disk test was applied to investigate the tribological behavior of the coatings, the friction factor of the coatings without microblasting and with microblasting at pressures of 2, 4, and 6 bar was 0.3, 0.27, 0.23, and 0.5, respectively. The wear resistance showed a 10 and 23% increment in the samples microblasted at 2 and 4 bar compared to the one which was not microblasted due to the rise of hardness and resistance against plastic deformation. At the pressure of 6 bar, however, the wear resistance showed a decrement due to the declined resistance against plastic deformation and the rise of surface roughness. Therefore, the optimal microblasting pressure was 4 bar. The corrosion behavior of the coatings was also explored by electrochemical impedance spectroscopy (EIS) and potentiodynamic polarization (PDP) in a NaCl solution (3.5 wt.%). The EIS results showed the highest RP (2425 ×103 .cm2) at the microblasting pressure of 2 bar, indicating the highest corrosion resistance after 24 hours of immersion. The PDP diagrams also revealed that the sample microblasted at the lowest pressures (2bar) had the lowest current density (0.0063 µA.cm2), corresponding to the highest corrosion resistance. Therefore, the optimal pressure of 2 bar can be proposed for the corrosion tests
فایل: ّFile: Download فایل